Vous avez besoin de prouver la fiabilité de votre projet ? Améliorer sa qualité est au coeur de vos préoccupations ? Vous êtes dans une démarche d’amélioration continue ou d’anticipation des risques ? L’Analyse AMDEC produit est l’outil dont vous avez besoin.
AMDEC et AMDEC Produit
Née dans les années 40s, aux Etats-Unis, elle arrive en France dans les années 60/70s. S’inspirant de la NASA et des industries militaires américaines, les industriels français recherchaient un moyen d’anticipation, d’amélioration et de fiabilisation. Au fil des usages, l’AMDEC – Analyse des Modes de Défaillance, de leurs Effets et de leur Criticité – est devenue cet outil incontournable. Ce dispositif de supervision et d’analyse prévisionnelle des risques est une solution de pilotage de l’amélioration continue.
L’analyse peut bien sûr porter sur de nombreux éléments de l’organisation. Par conséquent, il existe plusieurs Amdec :
-
-
- Organisation
- Produit
- Processus
- Moyen
- Sécurité
-
Dans votre démarche d’anticipation et de fiabilisation, l’AMDEC produit, initiée dès la phase de conception, est un excellent outil d’aide à la décision. Elle est par ailleurs aussi une solution de prévention. De par son approche de la sécurité, elle est parfois confondue avec l’évaluation des risques. Les deux démarches sont complémentaires. L’analyse des risques s’attache uniquement aux dangers et donc à la sécurité. L’Amdec produit étudie l’intégralité de l’objet, sa sécurité mais aussi sa fiabilité et sa qualité.
AMDEC Produit ? Pourquoi faire ?
Nous l’avons vu dans la définition même de cet outil, toute entité industrielle cherche la satisfaction de ses clients tout en améliorant la fiabilité de son système, en réduisant les risques et les coûts et en optimisant les contrôles. C’est la base même de l’approche AMDEC Produit.
La Fiabilité du système
Un système est stabilisé lorsqu’il est fiable. L’AMDEC tend donc à développer cette fiabilité, voire à la démontrer. Cela concerne aussi bien les produits que les moyens de production. Cette démarche vous aide à identifier les défaillances possibles, leurs causes, leurs conséquences néfastes. Ces effets peuvent impacter le produit lui-même tout autant que son environnement, comme d’autres composants d’une architecture complexe par exemple. Mais l’AMDEC Produit va plus loin. Non seulement vous identifiez les dysfonctionnements mais également vous les caractérisez. C’est à dire que vous les hiérarchisez. En cela, l’AMDEC est une aide à la décision importante.
La Maîtrise des risques
Dès lors que vous avez identifié les défaillances potentielles, vous pouvez donc les prévenir. Grâce à l’AMDEC, vous pouvez mieux structurer votre démarche préventive. En effet, il ne s’agit pas seulement d’identifier des anomalies mais également de les comprendre en recherchant les causes et les effets. Ensuite, il faut encore définir leur sévérité. Enfin, la démarche AMDEC permet de proposer des correctifs.
L’Optimisation Continue
Pour qu’une démarche AMDEC soit pertinente, elle doit s’accompagner d’une optimisation permanente. Et cela passe inévitablement par une amélioration des contrôles. En analysant les causes des défaillances, il est possible de définir les moyens de les détecter. Dès lors, l’équipe qualité peut mettre en place des plans de contrôle sur lesquels les équipes pourront ensuite s’appuyer pour prévenir les dysfonctionnements. Surtout, ces plans de contrôle, qu’ils soient par attributs ou par mesure, normalisent et structurent votre démarche qualité. De ce fait, vos coûts sont optimisés par rapport à un contrôle à 100% ou lorsque les tests sont destructifs. Vous vous concentrez sur les points essentiels soulignés par l’analyse AMDEC.
Un autre levier est la mise en place de fiches de poste. Cet outil pédagogique permet de décrire précisément la mission de chacun et ainsi de pouvoir renforcer les contrôles qualité. Ces fiches peuvent être rédigée par exemple en s’appuyant sur une approche PDCA ou Roue de Deming, boucle vertueuse de l’approche qualité (Planifier-Développer-Contrôler-Ajuster)
En résumé, l’AMDEC Produit, c’est prévoir pour ne pas revoir. L’analyse des anomalies réalisée dès la phase de conception permet d’apporter des modifications à un stade très précoce. Cela évite d’engager des frais importants grâce à une détection anticipée des faiblesses de la conception. Elle doit donc être menée en parallèle du cahier des charges – AMDEC Conception – ou aussitôt choisies les solutions techniques.
Démarche inductive, rigoureuse et précise
Mise en Place
Une démarche AMDEC est avant tout une approche structurée de votre projet. Cela demande donc de la rigueur, de la méthodologie mais aussi une parfaite maitrise du sujet étudié, son fonctionnement et tout son environnement.
Identification
Pour s’assurer de bien mener l’étude sur l’essentiel, la première étape est de bien identifier le sujet, le périmètre de l’analyse AMDEC Produit et ses limites. Pour cela, il est possible de se référer au cahier des charges. En effet, ce cadrage projet définit entre autre la fiabilité objectée, la maintenabilité et la capabilité du produit. Ensuite, il s’agit également de définir le planning de travail et la méthode retenue pour la cotation de la criticité. C’est aussi préciser les moyens mis à disposition et évidemment la finalité de la démarche. Bref, c’est poser en amont tous les éléments qui permettront une analyse objective et acceptée ensuite.
Mode Participatif
Une seule personne ne peut maitriser tous les aspects du système. La base est donc de mettre en place un groupe de travail. Il réunira toutes les connaissances nécessaires : conception, fabrication, qualité, méthodes, achats, sav, experts techniques (internes ou externes), etc. L’objectif est de mettre en commun et confronter les connaissances de chacun pour une approche la plus exhaustive possible. L’un des acteurs est désigné comme animateur. Il conduit et anime les débats, donne le rythme et planifie les échanges, veille au respect du périmètre d’étude, éventuellement tranche en cas de désaccord.
Mener une analyse AMDEC est stratégique, prend du temps et mobilise des collaborateurs. Il est donc essentiel de s’assurer de l’implication et de la responsabilisation des participants.
Analyse du système
Cela signifie notamment lister tous les composants du système et identifier son environnement d’utilisation, direct ou indirect. Avoir une parfaite connaissance du sujet, c’est maitriser aussi toutes les fonctions attendues. Cela permettra au final d’identifier celles qui pourraient ensuite devenir défaillantes. Pour cela, l’équipe réalise une analyse fonctionnelle détaillée. Cette étude approfondie permet de bien entrer dans les détails de l’AMDEC Produit.
Analyse des Défaillances
Analyser les dysfonctionnements, c’est rechercher les modes, comprendre les causes et mesurer leurs effets.
Analyse des Modes
Tout d’abord, c’est quoi une défaillance ? C’est une action réalisée en-dehors de la norme de fonctionnement. Elle peut être de différents ordres :
– Absence totale de fonctionnement,
– Non respect du timing : la pièce n’agit pas quand elle doit le faire,
– Fonctionnement partiel, pas à 100% des capacités ou baisse des performances,
– Une altération du produit différente de celle calculée et validée,
– Création d’un phénomène comme une fuite, de la corrosion, des vibrations, etc.
L’équipe Amdec va donc lister toutes les défaillances possibles. Bien sûr elle commencera par identifier tous les dysfonctionnements déjà connus. Elle va également dresser la liste de tous les points critiques, aussi bien du produit lui-même que de son environnement d’utilisation. Grâce à ce travail, elle pourra cumuler un maximum d’information sur les modes de défaillance, leur fréquence et leurs conséquences. En résumé l’analyse doit aussi bien être qualitative que quantitative.
Analyse des Causes
Une fois un problème repéré, pour le résoudre et l’anticiper, il est nécessaire d’identifier toutes les causes qui ont une influence plus ou moins directe sur le dysfonctionnement constaté. Elles peuvent être :
- Internes ou initiales, c’est à dire propres au produit lui-même,
- Dues au matériel amont au système,
- Attribuables aux interactions avec son environnement d’utilisation,
- Etre la résultante d’une action humaine (main d’œuvre).
Un outil d’analyse souvent utilisé en gestion de projet et recherche qualité est le diagramme d’Ishikawa ou Analyse des 5M : Moyens, Méthodes, Matériels, Milieu, Main d’Œuvre.
Analyse des Effets
Evaluer les effets des défaillances, c’est considérer les conséquences de ces anomalies sur tous les composants et sur le fonctionnement global du système. Il est donc essentiel de bien les mesurer à tous les niveaux fonctionnels. Nous pouvons donc identifier 3 typologies d’effets :
– Local : sur le produit et ses composants directs,
– De zone : sur le système et son fonctionnement,
– Global : sur l’intégralité de l’environnement d’utilisation.
Evaluation de la Criticité
Caractériser la criticité de chaque défaillance permet de hiérarchiser leur degré d’importance. L’Amdec Produit étant un outil d’aide à la décision, le décideur pourra ensuite définir son plan d’action pour, par exemple, agir en priorité sur les dysfonctionnements les plus critiques.
L’évaluation de la criticité est une solution objective qui s’appuie sur 3 critères stratégiques, évalués selon une échelle de grandeur définie lors de la mise en place :
– La Gravité/sévérité de la panne et son impact sur le produit, notée par exemple de mineure à grave,
– La Fréquence ou probabilité que la défaillance survienne, chiffrée de Improbable à très probable,
– La Détection ou l’aptitude à détecter cette déficience, estimée de aisée à délicate.
On obtient ainsi une matrice de criticité, dont les niveaux d’acceptabilité auront été une fois encore définis en amont par l’équipe de travail. Les niveaux d’acceptation peuvent être différents selon l’expérience, la “culture” d’entreprise, la typologie produits (jouet, médical, aéronautique, etc.). Si l’évaluation est plus ou moins subjective, la caractérisation de la criticité est la résultante d’un calcul objectif : Gravité x Fréquence x Détection.
Actions correctives
Désormais, le travail de l’équipe est de définir comment et où agir face à ce constat. En effet, une fois les points critiques identifiés, il convient d’engager les actions nécessaires avant la validation finale des choix techniques. Les actions correctives ont 3 objectifs principaux :
-
- Précaution = Eliminer les défaillances,
- Protection = Limiter les effets et donc la gravité,
- Prévention = Réduire la probabilité.
Pour ce faire, il est essentiel d’agir sur tous les leviers aussi bien de la conception que de l’usage, sans oublier bien sûr la production. Cela va reposer sur une articulation en 4 étapes :
-
- Définir les actions,
- Planifier le plan d’action,
- Formaliser les actions,
- Suivre le plan.
Au final, le plan d’action sert à documenter le processus de développement pour
-
- Perfectionner la conception dans une démarche d’optimisation continue,
- Définir les moyens de se prémunir contre les défaillances et leurs effets,
- Optimiser les tests pour s’assurer qu’ils permettent la détection des dysfonctionnements,
- Prévoir les redondances.
Matrice AMDEC Produit
Une matrice met en exergue les actions prioritaires à mener en fonction des niveaux d’acceptation. Dès lors, l’équipe peut être amenée à reprendre la conception.
Tout au long du projet, l’équipe AMDEC Produit renseigne le tableau de synthèse récapitulatif, véritable photographie de tous les éléments collectés :
- Composantes du système étudié,
- Fonctions attendues,
- Défaillances constatées,
- Mode de détection identifié,
- Causes repérées,
- Effets relevés,
- Criticité évaluée,
- Mesures correctives envisagées
Ce tableau sert de suivi et “vit” avec le projet. Si une criticité est trop élevée, l’équipe corrige : conception, détection, niveau d’acceptabilité, etc.
L’AMDEC Produit permet de valider le produit et sa conception, d’anticiper et corriger en amont les dysfonctionnements. Elle limite les constats matériels sur les prototypes ou les tests terrains sur échantillons initiaux (EI). Elle doit toujours s’accompagner d’un document de travail. L’analyse identifie les défaillances, leurs causes et effets mais elle établit également un plan d’action. Or ce dernier donne lieu à divers documents stratégiques : plan de fiabilisation, de contrôle qualité, de maintenance préventive, de surveillance, d’essais, etc.
Le travail ne doit pas s’arrêter là. Il est évident qu’il est indispensable de mettre également en place un plan de suivi rigoureux : suivi des défaillances, des actions correctives et de leurs effets aussi.
Chez HOGGAR Solution, nous considérons que pour finaliser l’analyse AMDEC, il est essentiel de remplir le tableau de suivi à partir de tests terrains à l’aide de prototypes ou d’EI. Cette phase est selon nous incontournable pour proposer un produit fiabilisé et stable. Ces tests doivent être menés graduellement et en situation client. HOGGAR Solution réalise ce type de tests pour vous. Ne pas les mener permet certes de mettre votre produit plus rapidement sur le marché mais cela peut être lourd de conséquences : risque de SAV, insatisfaction client, impact sur l’image du produit et de la marque, coûts très élevés.
HOGGAR Solution vous assiste – à la carte – pour chacun des éléments de l’analyse AMDEC ou pour un accompagnement global.
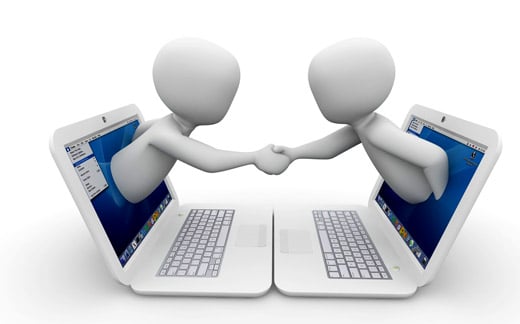
Prenons rendez-vous
Alors, prenez contact dès à présent pour nous soumettre vos besoins. Une réponse vous est apportée très rapidement.