Dans un contexte incertain, tendu et inflationniste, les industriels se remettent inévitablement en question quant à leur efficience. Les méthodes d’industrialisation et de production sont passées au peigne fin afin de produire mieux et au plus juste. C’est le principe du Lean Manufacturing. L’objectif de cette méthode d’organisation est d’optimiser la performance industrielle en partant toujours des exigences du client.
Qu’est-ce que le Lean Manufacturing ?
Données de départ
Produire mieux en partant du point de vue du client, cela signifie produire ce que veut le client, au moment où il le veut et pour le prix qu’il est prêt à payer. On pense immédiatement à :
-
-
- Limiter les superflus : ne produire que ce que le client veut et optimiser les stocks ;
- Eliminer tous les gaspillages inhérents au process de production. Cela concerne les dépenses inutiles en matériel, temps, mouvements, main d’œuvre, etc. ;
- Se concentrer sur ce qui crée de la valeur pour répondre aux besoins du client en termes de coût, qualité et délais.
-
Engager une démarche Lean vise à améliorer les processus de fabrication – l’industrialisation – pour répondre au client et renforcer sa rentabilité et son efficience. Au final, le Lean Manufacturing développe :
-
-
- Productivité grâce à une optimisation de l’efficacité,
- Qualité du produit en répondant précisément au cahier des charges et en réduisant les rebuts,
- Flux de matériel en livrant au bon endroit, au bon moment et en quantité suffisante.
-
Flexibilité, réactivité et production à la demande des industries Lean s’opposent à la standardisation et la production de masse des industries d’après-guerre.
Pourquoi faire du Lean Manufacturing ?
La démarche de Lean Manufacturing s’inscrit directement dans une volonté d’amélioration continue de l’industrialisation. Plusieurs objectifs sont visés :
-
-
- Satisfaire le client au plus près de ses besoins et attentes,
- Augmenter les tâches à valeur ajoutée,
- Réduire les gaspillages qui impactent la productivité,
- Développer la compétitivité de l’entreprise en augmentant sa flexibilité et sa réactivité,
- Rechercher la performance grâce à une qualité obtenue en utilisant moins de ressources,
- Viser les 5 zéros : 0 délai, 0 stock, 0 papier, 0 défaut, 0 panne.
-
Le Lean Manufacturing doit aussi être considéré comme un outil offensif puisqu’il donne un avantage concurrentiel. En livrant au plus juste, les clients sont satisfaits et se fidélisent.
Lorsque l’on se penche de près sur son industrialisation ou organisation industrielle, inévitablement, la philosophie du Lean Manufacturing est abordée. L’objectif reste toujours la recherche constante de l’efficience via différentes méthodes d’amélioration.
Avantages du Lean Manufacturing
Une entreprise qui applique une approche Lean Manufacturing est plus Agile car elle fabrique avec moins de ressources. Elle s’adapte aussi plus facilement aux évolutions de son marché. Enfin en utilisant moins de ressources, elle répond aux nouvelles exigences environnementales attendues par les consommateurs.
La démarche Lean s’appuie sur une volonté de prévention, d’anticipation et d’amélioration continue. L’approche est donc positive contrairement à la prise en charge de défaillances et non-conformités. L’effort est concentré sur la gestion de la création de valeur et repose sur un partage de la connaissance.
Son impact est aussi positif au niveau social. En effet, l’approche se penche sur les différents postes de travail et tend à les améliorer en réduisant les gestes inutiles et fatigants ainsi qu’en optimisant l’ergonomie. Enfin, en améliorant les coûts, on augmente la rentabilité et de ce fait, on lutte plus efficacement contre les délocalisations.
Lean Manufacturing et amélioration continue
1. Diagnostic des flux : flux de matières et d’informations de la commande client à la livraison du produit. Cette étape mobilise de nombreux services internes : achats, production, qualité, méthodes, logistique, etc. Mais aussi flux de valeur : identifier ce qui crée de la valeur dans toute la chaine d’industrialisation notamment.
2. Analyse du diagnostic : source de gaspillages, de pertes de temps, d’optimisation des coûts, de la qualité, des délais.
3. Recherche de solutions : L’objectif sera d’agir sur :
– La qualité :
> Réduire les gaspillages,
> Diminuer les erreurs, non-conformités, rejets, etc.
– Le coût :
> Produire uniquement le besoin,
> Consommer moins de ressources.
– Les délais :
> Favoriser l’écoulement des flux,
> Renforcer le JAT (Juste à Temps).
4. Amélioration continue. Bien sûr, l’approche doit rester sous surveillance voire être étendue à d’autres services que la production. On parle de Lean Management et/ou de Culture Lean.
Gaspillages ou Muda dans le Lean Manufacturing
L’identification des gaspillages en langage Lean est aussi appelée Muda. 8 catégories de gaspillages sont généralement reconnues:
1. Surproduction : principe même de la production de masse excessive par rapport aux besoins ;
2. Temps d’attente : tous les moments stériles qui ne génèrent pas de valeur ajoutée et nuisent à la fluidité de la production ;
3. Transports : déplacements qui consomment de l’énergie sans créer de valeur et font perdre du temps ;
4. Stocks inutiles et excédentaires souvent liés à la surproduction. En plus de ne générer aucune plus-value, ils engagent des immobilisations de capitaux, une prise de risque importante, de l’espace occupé et génèrent un risque de destruction des invendus ;
5. Opérations inutiles dans les process de fabrication du fait d’évolutions technologiques résultant d’habitudes ou de l’absence de mises à jour des gammes ;
6. Mouvements, notamment humains qui pourraient être supprimés car fatiguent inutilement la main d’œuvre, sont une perte de temps et sans objet ;
7. Pièces défectueuses ou erreurs. La non-qualité et/ou non-conformité génère des coûts de retouche ou de mise au rebut importants. Elle mobilise aussi de nombreuses ressources ;
8. Potentiel humain étouffé par une hiérarchie trop verticale. Cette approche qui ne s’appuie pas suffisamment sur la créativité et l’investissement des équipes ferme des opportunités. Elle est un gaspillage car c’est une sous exploitation des compétences.
Aux Muda, nous ajouterons aussi deux autres familles de gaspillages :
- Muri : l’ensemble des tâches trop compliquées ou chronophages ;
- Mura : les non-conformités, irrégularités donc les déchets potentiels.
La phase d’étude et d’analyse est essentielle. Hoggar Solution part d’une simulation de votre process industriel existant pour mettre en avant vos points forts et les points de tension. La gestion des flux, des process, des ressources est scrutée pour mieux identifier les points d’amélioration et de rationalisation.
Les Outils du Lean Manufacturing
Il existe de nombreux outils de diagnostic, indicateurs de performances ou KPIs. La plupart ont en commun l’identification des gaspillages, l’optimisation des flux et l’amélioration continue.
Nous allons présenter :
- Méthode des 5S se concentre sur le poste de travail ;
- Cartographie VSM analyse l’intégralité du circuit du produit, de la matière au client ;
- Approche Six Sigma rationalise et optimise les processus.
Méthode des 5S
Ou comment agir sur l’environnement de travail. Cet outil cherche à analyser comment améliorer les postes de travail des collaborateurs à partir de 5 principes :
o Supprimer le superflu et ne garder que le fondamental,
o Situer ou ranger pour ne plus chercher,
o Nettoyer pour mieux détecter les anomalies et usures prématurées,
o Standardiser les règles avec des repères pour mieux les partager et les appliquer,
o Suivre les actions, faire adhérer les équipes et si besoin améliorer.
Cette méthode limite les gaspillages et sécurise les zones de travail. En outre elle stimule les équipes qui travaillent dans un environnement plus agréable. Elle peut intégrer d’autres outils comme le Gemba – qui désigne où se crée la valeur – et le Kanban qui cherche à réguler les flux.
Cartographie VSM
Value Stream Mapping
En français, on parle de la cartographie des chaines de valeurs. Pour faire simple, l’équipe Lean analyse les processus pour mettre en exergue les gaspillages pour ensuite pouvoir les éliminer. Le travail d’analyse porte non pas sur un poste ou une machine en particulier mais bien sur l’ensemble du cycle du produit jusqu’au client. Par contre la démarche se concentre généralement sur un produit ou une famille de produits.
Toutes les catégories de gaspillages sont passées au peigne fin : les temps d’attente, cadences, temps de cycle, mouvements et gestes superflus, etc. C’est donc un travail de collecte terrain avant tout. Il faut véritablement se baser sur du concret et non sur des impressions. S’il est nécessaire de créer une équipe pour réaliser l’intégralité de la VSM, tous les membres n’ont pas besoin d’être sur le terrain. Mais au moins une personne doit absolument suivre l’entièreté du processus.
L’objectif est de lister toutes les opérations à valeur ajoutée et celles sans. Attention, en Lean, on se place toujours du point de vue du client. Donc la création de la valeur aussi.
C’est bien sûr un très bon outil d’étude des flux aussi bien matières, produits qu’informations. L’analyse des données collectées permet d’identifier les points d’amélioration pour épurer au maximum la chaine de production en se limitant aux opérations créant véritablement de la valeur.
Discipline et Application
La démarche requiert une grande rigueur, une méthodologie bien définie et un périmètre parfaitement identifié. Pour une collecte d’information la plus précise et fidèle possible, la participation et l’adhésion des équipes sont essentielles. Elle mobilise aussi du temps et des personnels formés. Donc il est nécessaire de bien analyser en amont les bénéfices qu’elle peut apporter et ne pas partir trop grand tout de suite.
Souvent les résultats sont exprimés sous forme de schémas. La représentation visuelle facilite la compréhension et donc l’implication. Il existe des conventions sur les symboles utilisés. Généralement ils sont articulés autour de 4 catégories : processus, marchandises, informations et général. Plusieurs exemples sont disponibles ICI.
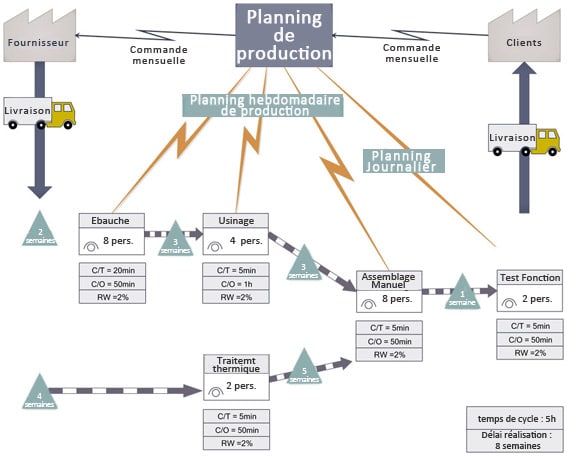
Six Sigma
Il s’agit ici d’améliorer la qualité de la production. Pour faire simple produire mieux, plus vite, à coûts maitrisés sans altérer la qualité. C’est plus un outil de solution ou de résolution de problèmes que de diagnostic.
L’analyse Lean cherche à réduire les gaspillages. Le Six Sigma vise le zéro défaut.
Vous pouvez aussi devenir Lean Six Sigma.
L’approche Six Sigma agit sur la variabilité de la qualité. Elle tend à homogénéiser la qualité de la production afin de réduire cette instabilité. Elle permet d’atteindre une certaine constance qualité et donc la satisfaction du client. En agissant sur la qualité, elle renforce la compétitivité et la prospérité de l’entreprise.
Si elle est très positive, elle est aussi très complexe à mettre en œuvre. Elle s’appuie déjà sur tous les outils de diagnostic de l’approche Lean. Elle requiert une certaine expérience dans l’analyse des données et des solutions à mettre en œuvre pour atteindre l’objectif. L’équipe doit avant tout trouver des axes d’amélioration en adéquation avec le profil de l’entreprise.
Le Six Sigma s’appuie beaucoup sur la méthodologie DMAIC :
Comment agir “Lean Manufacturing” ?
Agir pour Optimiser
La méthode Lean s’appuie sur 5 piliers qui lui permettent d’agir et d’optimiser la production.
Travail Standardisé
la standardisation du travail et non du produit. La démarche Lean veut que tous les postes de travail soient documentés et détaillés. Ainsi quel que soit l’opérateur, la méthodologie de travail reste la même. Elle est surtout la résultante d’une réflexion menée en amont pour rendre chaque poste efficient.
Takt Time
Les cadences de production sont calées sur la variabilité de la demande. L’objectif est de produire exactement ce que le marché demande, pas plus, pas moins. Dit autrement, c’est adapter sa capacité de production à la demande client. Finalement déterminer le Takt Time c’est déterminer la cadence qui optimise sa capacité à répondre à la demande sans générer de surplus. Pour le calculer au plus juste, il faut néanmoins le contextualiser, considérer uniquement le temps de travail créateur de valeur (donc hors pauses, maintenance, etc.).
Pull System
Une fois encore, la production est adaptée à la demande. On produit l’article réclamé par le marché. Cela nécessite une grande adaptabilité des équipes et des outils de production. La décision de produire ne repose plus sur des prévisions mais sur une demande réelle. Non seulement cela permet d’optimiser les ressources, de limiter le risque de surstockage mais cela implique de travailler en juste à temps. Au final, ce sont également les écarts financiers qui sont réduits. Bien sûr, il est indispensable de mettre en place un flux efficace et organisé.
Andon
L’Andon est un système d’alarme. Il peut être lumineux et/ou sonore. Il identifie un problème et accélère donc la capacité à le résoudre, donc la réactivité des équipes. Attention, on parle de signal d’alarme et non pas de signal d’urgence. Il ne doit pas se déclencher uniquement en cas de problème grave mais dès qu’une défaillance est détectée. L’objectif de l’Andon est de rapidement identifier un dysfonctionnement pour le résoudre au plus vite et revenir à une situation normale immédiate. L’Andon s’appuie donc sur du personnel formé et informé.
Poka Yoke
ou comment prévenir l’erreur. L’idée est d’éviter que l’erreur puisse se produire et réduire le besoin de contrôle des non-conformités. Ce pilier de la qualité est généralement utilisé là où il y a une intervention humaine : montage, branchement, assemblage de sous-ensembles, etc. Finalement, son but est de prévenir l’erreur humaine, par exemple en cas de fatigue, de défaillance de concentration, de manque de compétences, etc. En amenant le risque d’erreur à une valeur proche de 0, le Poka Yoke permet aussi de réduire le risque d’accident. Bien sûr, pour le mettre en place, nous devons parfaitement analyser le poste, identifier les erreurs possibles, leurs causes et définir les moyens de les supprimer. Au final, le Poke Yoke s’attache à travailler en amont en évitant les erreurs plutôt qu’en aval en ajoutant une étape de contrôle. Les erreurs potentielles peuvent être extraite d’une AMDEC produit ou processet/ou d’une analyse de risques.
L’accompagnement Lean Manufacturing Hoggar Solution
Notre Approche Lean Manufacturing
Hoggar Solution aide ses clients à identifier en premier lieu les processus qui peuvent changer et ceux qui devront changer. Notre objectif est la réussite de votre démarche. Cela doit donc passer par l’adhésion de vos équipes. Il est pour nous essentiel d’avancer progressivement dans le respect de vos contraintes, de votre culture et de votre organisation. Privilégier le step-by-step garantit davantage la réussite de la démarche que de faire table rase et voire trop grand trop vite. L’industrialisation est un segment très sensible qu’il convient de modifier avec prudence et pertinence.
Notre intervention
– Analyse : notre regard critique extérieur va chercher vos points forts et identifier les différents gaspillages. A l’aide de plusieurs outils, nos équipes identifient également les postes de dépenses excessives pour vous aider à adapter vos moyens à vos besoins. Nous analysons également votre gestion des flux ;
– Représentation : Si vous ne disposez pas déjà des éléments, ensemble nous représentons votre situation de départ : plan de masse, d’implantation, de flux, etc. ;
– Recherche de solutions : qu’il s’agisse de modéliser votre implantation pour améliorer les flux, intégrer de nouveaux postes à l’existant, d’améliorer ou créer des postes de travail adaptés, mettre en place des solutions modulaires et/ou nomades, etc., nous vous apportons un schéma d’amélioration personnalisé et adapté ;
– Mise en oeuvre : ensemble nous construisons la nouvelle organisation pour un flux optimal du stock de matières premières au chargement des produits finis : préparation de la commande, prélèvement matières, usinage, équipements standards, etc. ;
– Elaboration : les ingénieurs Hoggar Solution réalisent et rédigent pour vous les cahiers des charges de chacun des postes ;
– Exécution : A partir de nos cahiers des charges vous pouvez consulter vos propres partenaires ou poursuivre avec nos équipes pour le chiffrage, l’étude et la réalisation de vos différents postes de travail optimisés Lean.
Lean Engineering
L’accompagnement Hoggar Solution dans votre démarche Lean Manufacturing se situe aussi encore plus en amont via le Lean Engineering. En effet, il est important de considérer le « produire juste » dès la phase de conception des articles à produire. Avant de produire bien il faut concevoir au plus juste.
Le Lean Engineering consiste à concevoir de façon à :
– Supprimer l’inutile,
– Anticiper la simplicité de production,
– Imaginer le processus de production le plus efficient : “Design for manufacturing, Design for assembly, Design for cost”
– Produire sans perte de matière, d’énergie, de main d’œuvre, de temps, etc.
– Préserver la productivité des équipements en considérant leur maintenance.
Hoggar Solution travaille également avec vos équipes pour répondre à votre recherche de progrès permanent en apportant des solutions concrètes, reproductibles et durables. Notre approche n’est pas seulement curative mais s’inscrit également dans une volonté préventive que ce soit lors de la conception de vos produits, de la mise en place de vos process ou encore pour le développement de nouvelles activités.
Conformément à notre ADN, nous vous proposons aussi bien des solutions à la carte que des kits clé-en-mains pour développer votre compétitivité opérationnelle.
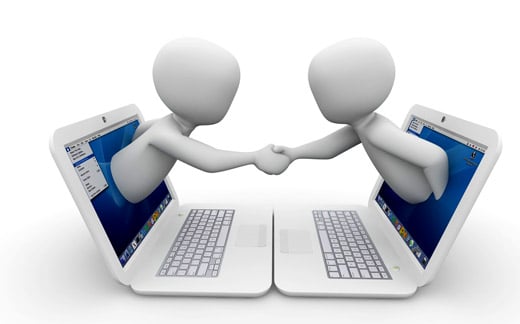
Prenons rendez-vous
Alors, prenez contact dès à présent pour nous soumettre vos besoins. Une réponse vous est apportée très rapidement.